Thermal Imaging Diagnostics: Your Reliable Partner in Electrical Equipment Maintenance
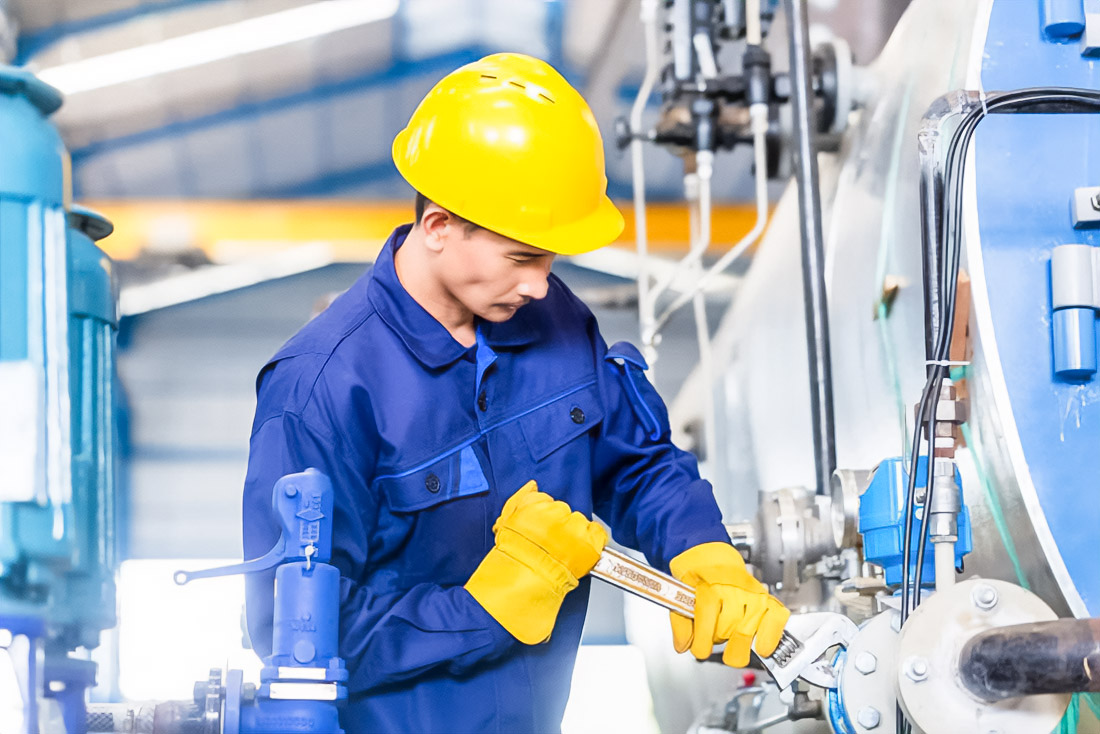
Thermal imagers — these are high-tech devices functioning on base infrared radiation. Infrared radiation is present in all bodies with temperatures above absolute zero (0 K or -273.15°C). Modern thermal imaging cameras capture this radiation and convert it into images, where color scheme displays temperature differences. Law Planck becomes the key theoretical foundation for these processes, describing how intensity radiation varies with temperature.
Technical capabilities thermal imagers impress: they can detect changes in temperature up to several tenths fraction of a degree. Thanks to this, they recognize areas of overheating in electrical systems, which is extremely important for preventing accidents. Modern models and thermal imagers work in expanded range temperatures, which makes them universal solutions for the inspection of complex electrical installations. For more effective maintenance worth pay attention to mechanical and electrical services.
Why Thermal Imaging Diagnostics Impossible without Advantages?
Introduction Thermal imaging diagnostics promises many advantages. In 2022, the market for equipment for thermal imaging diagnostics amounted to more than 2 billion dollars, which is a testament to the high demand and trust for this technology. Consider key advantages of using thermal imaging cameras:
- Prevention disasters: Detection abnormal temperatures allows prevent accidents. For example, research in the year 2023 showed that in 78% of cases, thermal imagers in advance indicated hidden problem connections.
- Increase safety: Minimization risks, such as fire, constitutes a priority task. In conditions that work with high-voltage installations, this, in 64% of cases, allows avoiding serious accidents.
- Savings on maintenance: Optimization schedules maintenance and reduction expenses on repair leads to 25%-th savings budgets companies.
- Increase longevity equipment: Timely elimination malfunctions increases service life equipment on 30%, saving millions dollars on replacement equipment annually.
How Used Thermal Imaging Diagnostics in Practice?
Thermal imaging diagnostics has mass practical applications in various fields of power engineering. Consider examples of successful its use:
- Overheating connections: Poor contact, for example, in connections with large transformers, often leads to overheating. Detection of such points prevents potential accidents and saves companies up to $50,000 a year.
- Problems with insulation: Worn or damaged insulation wires can cause short circuits. Thermal imaging cameras identify leakage currents, reducing the risk of accidents. More about problems with insulation can be learned on page Wikipedia, dedicated to electrical insulation.
- Uneven load in transformers: Such unevennesses are detected by increased radiation heat from certain sections of the transformer. Balancing reduced accident events by 15% in companies where it applied.
- Electrical panels: Incorrect operation automatic breakers can also be determined with the help of thermal imagers. This allows avoid more serious breakdowns in the future.
Main Recommendations for Successful Thermal Imaging Diagnostics
Effective use of thermal imaging diagnostics is possible with compliance with certain recommendations. Here are several tips for successful implementation:
- Frequency inspections: Systematic checks — not less than one time in a year — obligatory. If the equipment works in conditions with increased load or is located in zone risk, it is worth increasing the frequency of checks to two times a year.
- Suitable equipment: Necessary quality thermal imagers with high resolution and support necessary temperature range. This is an important aspect of the accuracy of obtained data. Additional information about choice equipment available on ResearchGate.
- Training personnel: Employees must undergo training and qualification for work with infrared cameras. This will allow the situation to be adequately assessed and timely measures taken.
- Documentation: All inspections must detail document. This will help not only track dynamics changes but also build long-term strategies for the improvement of the reliability of technical systems.
Thermal imaging diagnostics — this integral element of modern maintenance electrical equipment. With its help, ensure safety, reliability, and longevity systems. Investing in this tool — this strategic choice pays off growth overall efficiency work energy installations.